prodotti boema / Potatoes Processing Lines / Pelatore a Vapore SPB, l'originale con cestello rotante
Pelatore a Vapore SPB, l'originale con cestello rotante
Principio di pelatura a vapore Boema S.p.A.
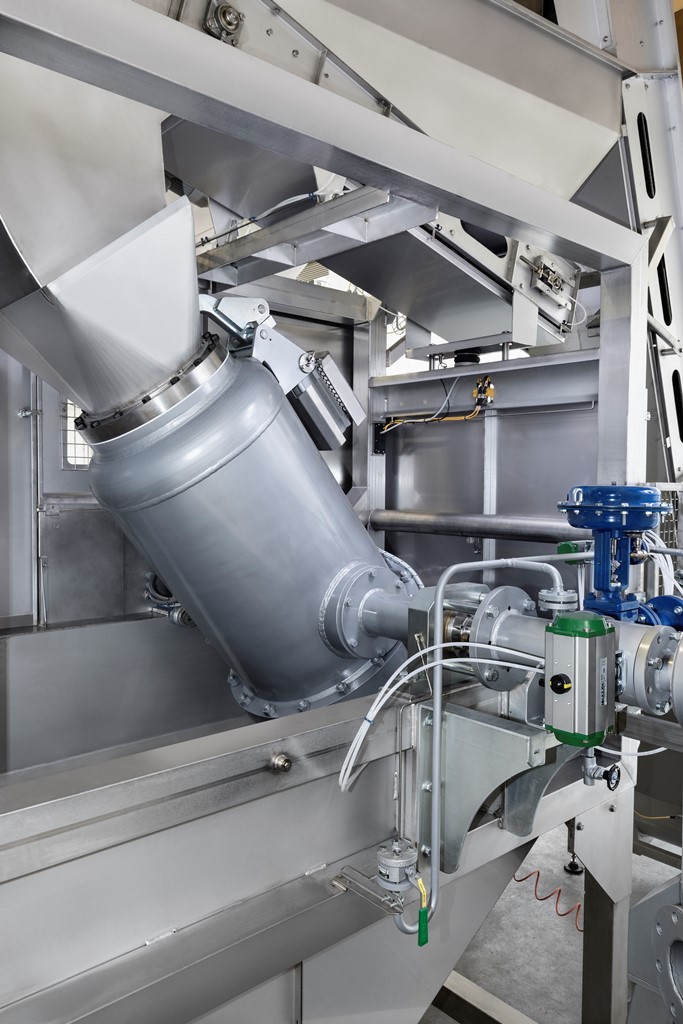
Boema costruisce pelatori a vapore che lavorano in batch secondo un ciclo così suddiviso:
1) CARICO PRODOTTO: Il prodotto, precedentemente caricato nella tramoggia superiore (che può essere dotata di proprie celle di carico per uniformare i batch), viene trasferito al contenitore di pelatura nel quale il cestello interno ruota per favorire la corretta distribuzione del prodotto all’interno.
2) ESPULSIONE ARIA: l’iniezione del vapore comincia mentre si sta ultimando il carico tramite un iniettore posto sul fondo del contenitore stesso. Grazie alla continua rotazione del cestello interno, questa fase è molto veloce (qualche secondo), inoltre la continua movimentazione del prodotto fa si che non si creino delle zone preferenziali per il passaggio del vapore ed evita la formazione di bolle d’aria intrappolate all’interno del contenitore.
3) CHIUSURA DEL CONTENITORE ED IMMISSIONE DI VAPORE: chiuso il portellone di sicurezza, il contenitore ruota in posizione orizzontale; intanto comincia l’immissione di vapore tramite il collettore di alimentazione principale posto all’interno del supporto di rotazione del contenitore. Il cestello interno continua a ruotare favorendo l’omogenea distribuzione del vapore tra il prodotto e nel frattempo inizia il carico della tramoggia superiore per il ciclo successivo.
4) PELATURA E PREPARAZIONE DEL CICLO SUCCESSIVO: raggiunta la pressione di vapore voluta e mantenuta per un tempo di permanenza pre-impostato, avviene la pelatura per effetto della repentina depressurizzazione del contenitore che provoca lo scoppio della buccia. Anche in tutta questa fase, il cestello interno continua a ruotare, svolgendo il duplice ruolo di favorire il distaccamento di tutta la buccia e d’impedire che parti di prodotto rimangano immerse nella condensa che si raccoglie sul fondo del contenitore, che annullerebbe l’effetto di depressurizzazione sul prodotto. Nel frattempo la tramoggia superiore è pronta per il successivo ciclo.
5) SCARICO CONDENSA, BUCCE E PRESSIONE INTERNA: grazie alla possibilità di ruotare l’intero contenitore del pelatore a pressione mod. SPB, facilita anche la fase di scarico che prevede prima una leggera rotazione verso l’alto del contenitore per facilitare lo scarico delle condense e delle bucce che si raccolgono sul fondo, successivamente avviene la rotazione verso il basso per lo scarico del prodotto.
6) SCARICO PRODOTTO: lo scarico del prodotto viene velocizzato dalla continua rotazione del cestello interno, e alla sua conclusione, il contenitore ruota nuovamente verso l’alto nella posizione di carico per il successivo ciclo di pelatura.
Le durate di alcune fasi del ciclo possono essere preimpostate dal PLC.
Il sistema del cestello rotante all’interno del pelatore porta numerosi vantaggi tra i quali ricordiamo:
- Ottima circolazione del vapore e penetrazione all’interno della massa di prodotto contenuto nel cestello;
- L’intercapedine tra cestello e parete del recipiente facilita la diffusione del vapore, che impiega meno tempo a raggiungere e riscaldare tutto il prodotto;
- La rotazione del cestello smuove il prodotto facilitando ulteriormente l’azione del vapore;
- Ottimo drenaggio della condensa: il prodotto da pelare non è mai sommerso dalla condensa e questo facilita lo scambio termico col vapore e aumenta la velocità di riscaldamento;
- La rotazione del cestello e l’intercapedine facilitano lo scarico del vapore;
- Si incrementa così il brusco salto di pressione necessario per il distacco “esplosivo” della buccia.
Perché scegliere un pelatore a vapore Boema?
I punti di forza dei pelatori a vapore Boema mod. SPB sono:
1) EFFICIENZA NEI CONSUMI: grazie ad una migliore diffusione del vapore e penetrazione intorno a tutto il prodotto, i pelatori a pressione di vapore Boema garantiscono le medesime rese di pelatura pur lavorando a pressioni di vapore inferiori rispetto a qualsiasi altro pelatore.
2) QUALITA’ DI RESA: grazie al cestello interno rotante, si migliora la diffusione del vapore e si evita che il prodotto rimanga troppo ammassato, favorendo la completa ed uniforme pelatura di tutto il prodotto all’interno del contenitore.
3) AFFIDABILITA’: i pelatori a vapore Boema mod. SPB sono realizzati in serie, seguendo progetti testati da anni di esperienza per tutte le applicazioni e sottoposti a carichi di lavoro molto pesanti.