products / Potatoes Processing Lines / STEAM PRESSURE PEELING FOR PEACHES
STEAM PRESSURE PEELING FOR PEACHES
Ecological steam pressure peeling for peaches
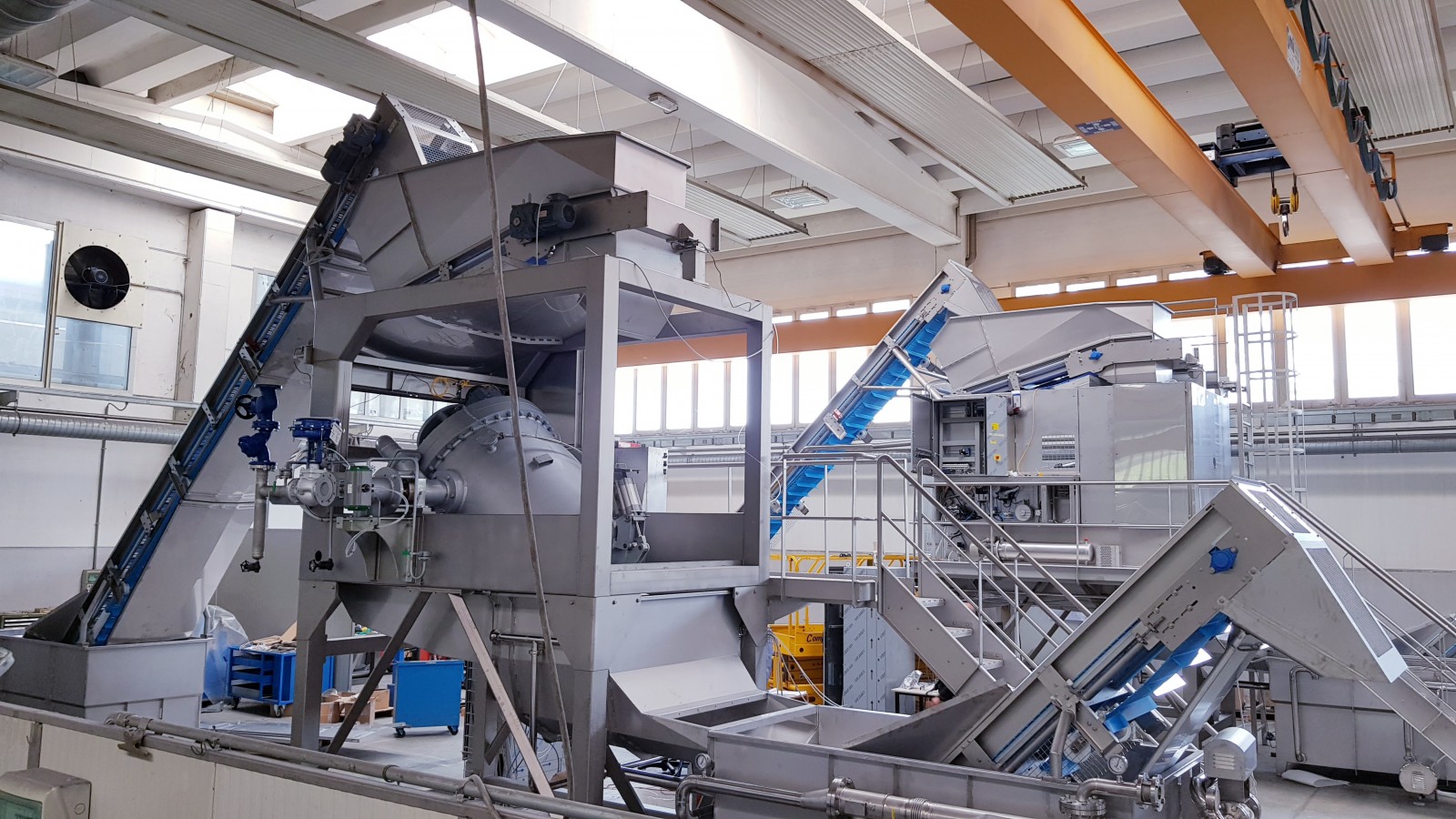
Boema exploits the steam pressure peeling for tubers and roots for the application on peaches. With the same standard working phases it is possible to peel the peaches by steam without the addition of chemical additives that could affect the taste and smell of the fruits. Starting from the conventional use of the machine, some purely mechanical setups are made to preserve the integrity of the peach, in order not to damage it or bruise it, since it is more delicate than tubers.
The work cycle is the following:
1) PRODUCT LOADING: the product, previously loaded into the upper hopper (that can be provided with own loading cells to uniform the batch), is transferred to the peeling tank, in which the inner basket rotates to facilitate the correct distribution of the product inside it.
2) AIR EXPULSION: the injection of steam begins when the loading is ending and it is made through an injector on the bottom of the container same. Thanks to the continuous rotation of the inner basket, this phase is really quick (it lasts few seconds), and furthermore the continuous moving of the product ensures that there are no areas in which the steam concentrates and avoids also the formation of air bubbles that could be trapped inside the container.
3) CONTAINER CLOSING AND STEAM ADMISSION: once the safety door has been closed, the container rotates into horizontal position; in the meanwhile, the steam admission begins by the main feeding manifold placed inside the rotation support of the container. The inner basket begins to rotate favouring the homogeneous distribution of the steam in the product and in the meanwhile begins the loading of the upper hopper for the following cycle.
4) PEELING AND PREPARATION OF THE FOLLOWING CYCLE: once the wanted peeling pressure has been reached and kept for the pre-set resting time, the peeling takes place thanks to the sudden depressurisation of the container, that causes the burst of the peel. Also during this whole phase, the inner basket continues rotating, both facilitating the detachment of the whole peel and avoiding that parts of product remain plunged into the condensates on the bottom of the container, thus annulling the effect of the depressurisation on the product. In the meanwhile, the upper hopper is ready for the following cycle.
5) CONDENSATE, PEELS AND INNER PRESSURE DISCHARGE: thanks to the possibility to turn the whole container of the steam pressure peeling machine mod. SPB, the discharge phase is facilitated: at first the container rotates slightly upwards to facilitate the discharge of condensates and peels on the bottom, then it turns downwards for product discharge.
6) PRODUCT DISCHARGE: the product discharge is speeded up by the continuous rotation of the inner basket. Once it is ended, the basket rotates again upwards to reach the loading position of the following peeling cycle.
The cycle time durations are preset by the PLC.